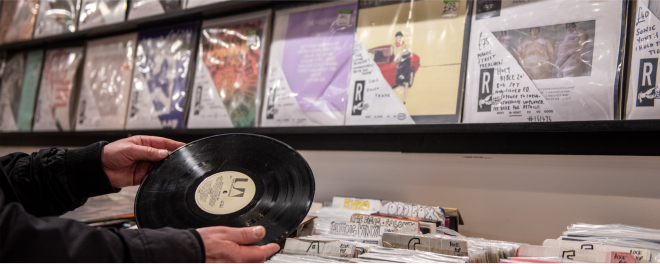
As vinyl sales continue to increase year to year, the Vinyl Record Manufacturers Association (VRMA) aims to bring awareness and advocacy to the industry. A professional trade association of independent businesses committed to the craft of vinyl record manufacturing, VRMA explains how vinyl is made in their guest piece for American Songwriter.
Videos by American Songwriter
[RELATED: Vinyl Sales See Significant Increase in 2023
Similar to songwriting, there is much craft and detail that goes into the handmade process of vinyl manufacturing. Below, the experts at the VRMA share a step-by-step process, including asset delivery, plating and stampers, test pressing, and quality control. VRMA President Dustin Blocker, who is also the Founder and CCO of Hand Drawn Records, teams with Echo Base’s Michael Greig Thomas, Welcome to 1979’s Bobbi Giel, and Gotta Groove Records’ Vince Slusarz to break down the process.
1. Asset Delivery: Best Practices for Receiving Artwork and Audio
Contributor: Michael Greig Thomas, Echo Base
When it comes to the production of vinyl records, attention to detail in asset delivery is paramount. Clients, including musicians and record labels, should not only provide their audio tracks but also deliver artwork that will grace the vinyl record jackets, inner sleeves, lyric inserts, posters, and stickers. These visual elements are as crucial as the audio itself in creating a captivating and immersive experience for fans and collectors. Some important tips include:
- File Formats: Clients should provide artwork in vector-based formats, such as Adobe Illustrator or scalable vector graphics (SVG). These formats ensure that the artwork can be scaled up without loss of quality, which is especially important for larger items like posters and the jacket itself.
- Colors: Clients should use Pantone colors for precise color matching. Using spot colors rather than process colors ensures that the final print accurately reproduces the intended colors.
- Bleed and Safety Margins: To ensure that no essential artwork elements are cut off during printing and assembly, clients should include bleed and safety margins in their designs. Furnace Manufacturing’s guidelines may specify these dimensions.
- Resolution: High-resolution artwork is crucial for sharp and clear printing. Furnace Manufacturing’s guidelines likely recommend a minimum resolution for images and graphics.
- Typography: The choice of fonts and text sizes should be legible and complement the overall design. Clients should consider readability, especially for lyric inserts and other text-heavy elements.
- Special Finishes: If clients wish to incorporate special finishes, such as embossing or foil stamping, they should work closely with the manufacturer to ensure that the artwork is prepared correctly to accommodate these features.
2. Asset Delivery: Best Practices for Receiving Audio
Contributor: Michael Greig Thomas, Echo Base
Regarding audio, preparing a vinyl master requires a distinct approach compared to digital releases. Vinyl records have specific attributes that must be considered during the mixing and mastering process. These attributes include:
- Dynamic Range: Vinyl has a limited dynamic range compared to digital formats. As a result, it’s crucial to ensure that the audio doesn’t have excessive peaks or dips in volume. Engineers often use specialized compressors and limiters to achieve a consistent dynamic range suitable for vinyl.
- Low-Frequency Management: Bass frequencies can be a challenge on vinyl due to the risk of causing the needle to jump or create distortion. Careful attention is paid to managing low frequencies, ensuring they are well-balanced and not overly dominant.
- High-Frequency Considerations: Vinyl records can lose high-frequency details, so engineers adjust the master to avoid excessive high-end content that might cause distortion or excessive surface noise.
- Centering and Phasing: Proper centering and phasing of the audio are crucial to ensure the needle tracks smoothly from the outer edge of the record to the center.
- Vinyl-Specific EQ: Mastering engineers may apply specific equalization tailored for vinyl, including RIAA curve adjustments, to compensate for the way vinyl records are physically played back.
In summary, clients should provide meticulously crafted artwork and high-quality audio masters that consider the unique attributes of vinyl. This attention to detail not only enhances the aesthetic and sonic quality of the vinyl record but also ensures a seamless production process that ultimately delights music enthusiasts and collectors alike.
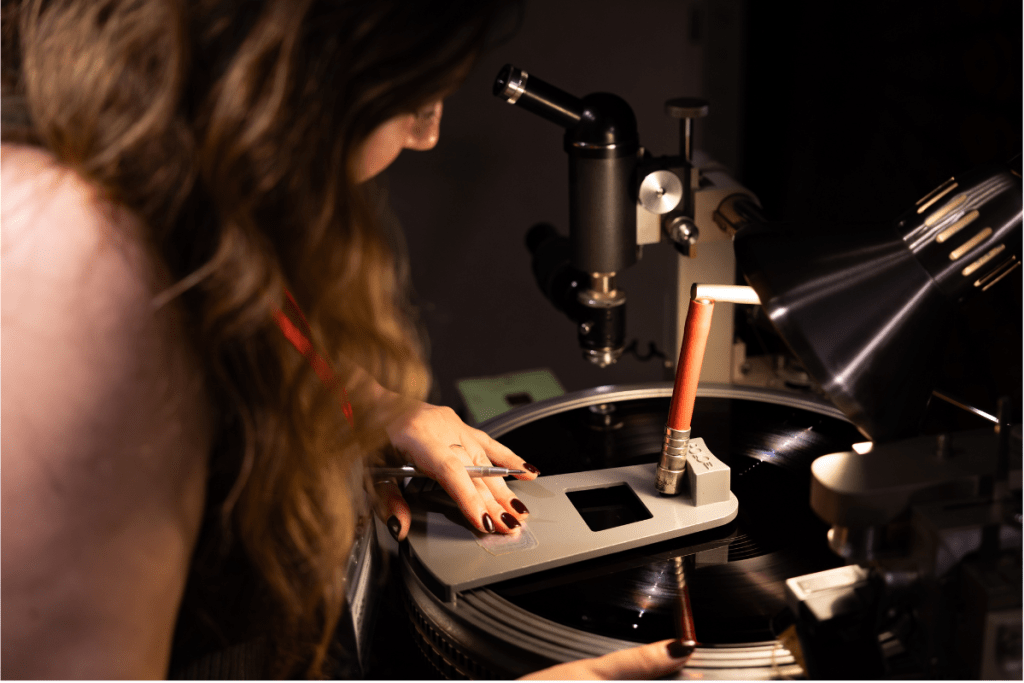
3. Cutting the Master
Contributor: Bobbi Giel, Welcome to 1979
Once audio is prepared for the vinyl format, it is then sent to a cutting engineer whose primary responsibility is to make sure the translation from the original source (i.e. the audio assets) to the lacquer master is not only as transparent as possible but also playable on the majority of consumer turntables.
The “lacquer master” often referred to during the vinyl manufacturing process is a 14” aluminum disc with a thin layer of nitrocellulose lacquer coated on both sides. The audio is engraved into the lacquer coating on a disc-cutting lathe using either a sapphire or diamond stylus. These lacquer-coated discs are fragile and highly flammable and therefore need to be handled with the utmost care throughout the production process. They are considerably malleable as well. To avoid risking the integrity of the audio (especially higher frequencies) by playing it back after it’s been engraved, cutting engineers inspect the grooves under a microscope to determine their playability.
The lacquer cutting process is not only the first step in the vinyl manufacturing process but also the last step in the creative process. The cutting engineer may make additional sonic changes (i.e. EQ, overall level, low-end imaging, etc.) to ensure the audio translates well to the lacquer even if the audio was prepared specifically for vinyl. However, once the audio is engraved into the lacquer disc, the record has entered the manufacturing stage.
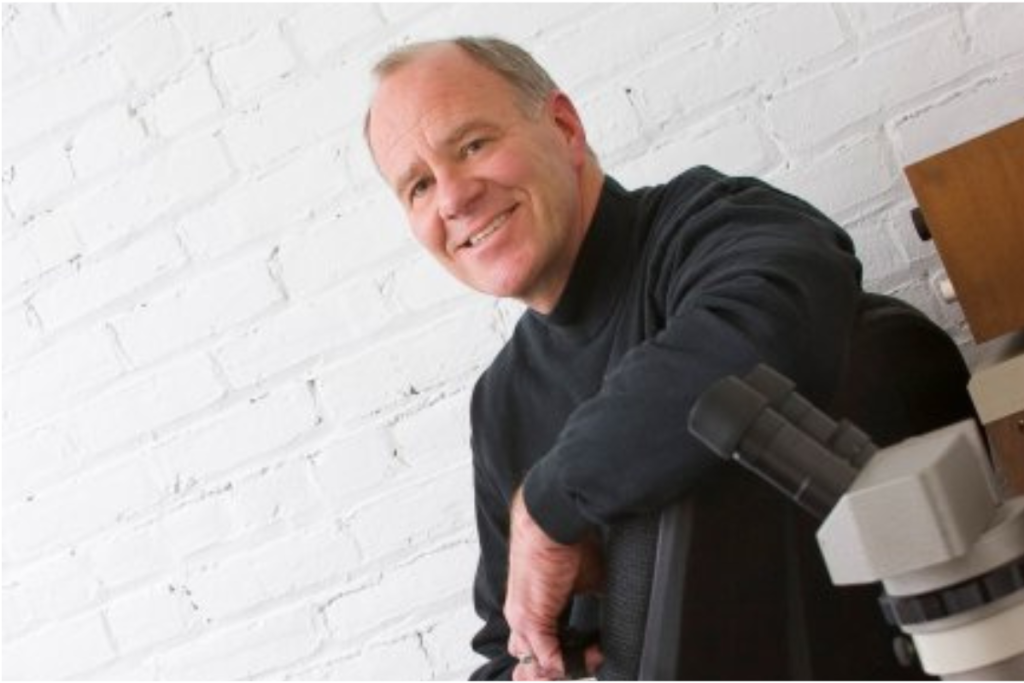
4. Plating and Stampers
Contributor: Vince Slusarz, Gotta Groove Records
After the lacquer is cut it is sent to a plant for a process commonly referred to as “record plating” (technically “electroforming”). The lacquer is inspected for any visible defects and prepped. It is then cleaned with detergent and water, rinsed, and sprayed with a silver solution to completely coat it.
The silvered lacquer is placed in a bath of dissolved nickel. An electrical charge applied to the bath fuses the nickel to the silvered lacquer. Once coated with nickel it is removed from the bath, and the nickel layer is carefully peeled from the silvered lacquer. This nickel part is the mirror image of the lacquer, so the grooves are raised.
This nickel part is then used as follows depending upon the subsequent process:
- One-step plating: The part is formed to the specifics of the die used in a record press, and is now termed a “Stamper.” The A side stamper is placed on the bottom die of the press; the B side is on the top, and the raised grooves of the stampers are imparted in the vinyl. While more economical for a short run of vinyl records, if the Stamper does not produce a record of acceptable audio quality or if it gets damaged, the lacquer must get recut and plated again.
- Two-step plating: The part is placed back in the nickel bath. Another layer of nickel is applied and then removed from the part. This removed new part is termed a “Mother,” with the original grooves again evident. The Mother is then inserted into the bath, and a layer of nickel is deposited and then removed to produce a Stamper. Multiple Stampers can be made from one Mother; since a Stamper has a finite pressing life (roughly 1000 press cycles) multiple Stampers are needed for larger runs of a vinyl record project.
- Three-step plating: Multiple Mothers can be formed from the original nickel part (in this process this original nickel part is termed a “Father”). These Mothers then can produce multiple Stampers; as with Stampers, Mothers have a finite life, so three-step is typically used for very large runs of a vinyl record project.
5. Test Pressing
Contributor: Vince Slusarz, Gotta Groove Records
The Stampers for the vinyl record project are provided to the pressing plant where they are examined for any visible defects. The A side Stamper is applied to the bottom die of the vinyl record press, and the B side Stamper is applied to the top die. The production labels for the project are not used, instead blank labels or labels identifying the record as a test press are employed. These test press labels are applied within the vinyl record press as several copies of the record are made.
The test press record is examined and listened to at the pressing plant. If the record passes the pressing plant’s quality standards, test press copies of the record (usually five) are sent to the customer, and one or more reference copies are kept at the plant. The customer must listen to and approve the test press before the production run is scheduled.
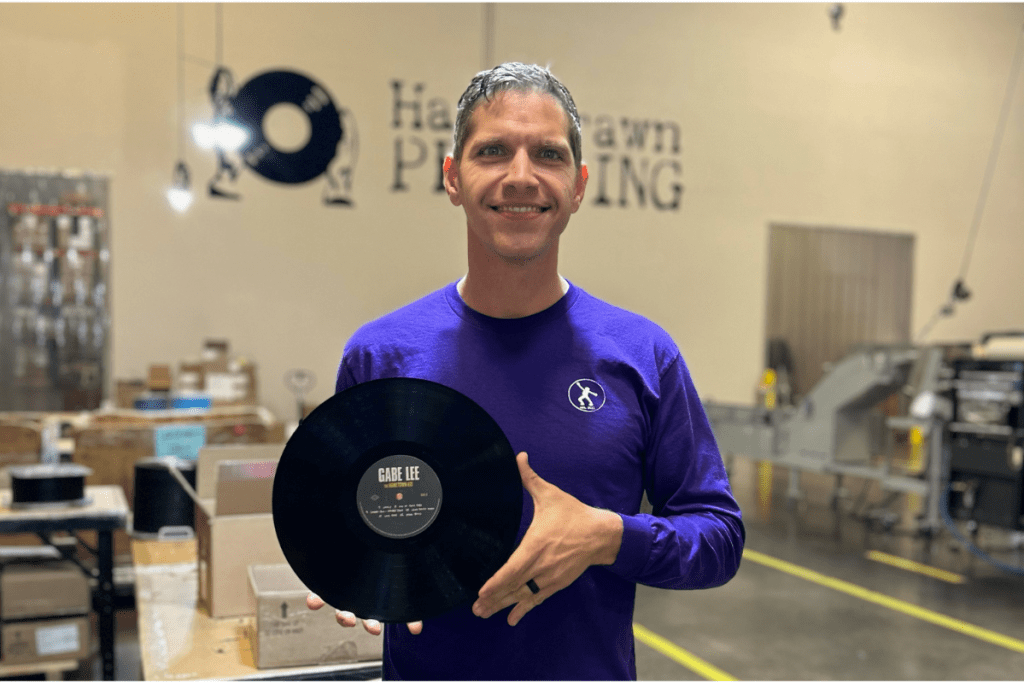
6. Pressing
Contributor: Dustin Blocker, Hand Drawn Pressing
At the vinyl record pressing plant, all of the final record production and assembly work takes place. Through the process of compression molding, polyvinyl chloride (PVC) is first melted with an extruder that feeds into the record press wherein the hot PVC is compressed in between two molds to form a vinyl record. After the record is formed, it is set onto a spindle to cool for several hours before the final QC and packing stages.
The varied colors of vinyl records come from the raw PVC and many of the custom-blended colors offered are typically hand-blended by the record press operators. To produce a high-quality vinyl record two key components are at play; the raw materials (PVC & stampers) and an operator’s craftsmanship and training. Operators and their quality assurance counterparts must work hand-in-hand to ensure both audio and visual quality are maintained throughout the production process.
7. Quality Control
Contributor: Dustin Blocker, Hand Drawn Pressing
Quality assurance and quality control at the pressing plant level are wildly important and unique in the process to each plant. Primarily, record press operators and quality assurance professionals are aligned in what is acceptable by the plant on both audio issues and visual blemishes, warpage, dishing, etc.
Ideally, the issues above should be minimal, but when a record fails quality control these are typically recycled in-house; and granulated back into raw PVC to be reused in the pressing process.
(Photo by Chris J Ratcliffe/Getty Images; All other photos courtesy VRMA)